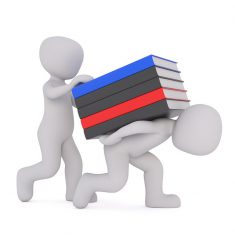
Everyone expects quality, whether it is of a new car, a bottle of wine, a heating system in a house, a hotel service or the delivery of a complex machine ready to start mass production. The criteria for measuring quality will always depend on the context. Quality cannot be strictly measured, but it can be evaluated. The quality of a product or service depends accordingly on the client requirements and how it fulfills their interests.
Quality Management Systems
There are several quality management systems that allow a variety of quality assessments. Formally, a system is a set of interrelated elements. That is, when we talk about a system, we are not just talking about a group of elements that are together, but elements that are also interconnected, all working together.
A quality management system is an operational working structure that is well documented. It is well integrated into the technical and managerial procedures that serve to guide the activities, bringing together workers, machinery, equipment, services, and the organization of information, in a practical and coordinated way, to ensure customer satisfaction and lower associated quality costs. These are systems of coordinated activities based on a set of elements (resources, procedures, documents, organizational structure and strategies) that aim to achieve quality products or services intended for a customer. In order to achieve the desired level of quality, a quality management system needs to plan, control and improve those elements of the company or organization that influence customer satisfaction.
Quality management systems are present everywhere, not only in the manufacturing industry but also within banks, insurance firms, real estate and construction companies, educational institutions, the food industry, healthcare and medical sectors, to name a few.
Quality also creates a competitive advantage. The total costs of a single product failure may be massive for an organization in repair and rework, in scrapping and waste, in shutting entire production lines, recalls, reputation, lost sales, or simply servicing warranties. The cost of quality is less than the cost of not investing in a quality system that guarantees a quality product or service in the long term.
Here is a brief description of some quality management systems or methodologies in use today.
- Six Sigma (6σ): This management system involves process improvement, statistical quality goals and quality management. Its core element is the description, measurement, analysis, improvement and monitoring of business processes using statistical methods. The methodology used involves the following steps: Define, Measure, Analyze, Improve, Control (DMAIC). The objectives are both focused on important financial and economic variables of the company and on customer needs.
- Lean manufacturing: This management system embraces operations, suppliers and customer relations. It requires less capital, less human effort, less space and less time to manufacture products with fewer defects, and according to precise customer specifications. It also focuses on the reduction of eight types of “waste” (transport, inventory, motion, waiting, overproduction, over-processing, defects, and under-utilized human talent) in manufactured products. Eliminating waste improves quality and reduces production times and costs. Tools used include continuous process analysis, production pull and fail-safe processes directly on site.
- Total Quality Management: This management system aims to raise quality awareness at all organizational levels and processes, and has been widely used in all sectors, from manufacturing to education, government and service industries. It is called "total" because it concerns the global organization of a company and the people working in it. Quality management should not be limited to technical functions to ensure product quality. It should be based on the relationship between the company and its customers. The primary goal is customer satisfaction, which can be permanently guaranteed only by a long-term development of the company itself. Total quality management aims to have customer satisfaction applied to both the product and the company. As the objective is customer satisfaction, this system aims to obtain benefits for all the company stakeholders. Therefore, the idea behind it is not only to manufacture a product to sell, but through continuous improvement, to improve working conditions and staff training so company employees engage at all levels to ensure optimum quality in all areas.
- Kaizen: This methodology can be described from an economic and behavioral perspective. A strategy that focuses on the continuous improvement of manufacturing processes, engineering and business management, it uses a “bottom-up” logic. Besides manufacturing, it has recently found applications in health care, psychotherapy, coaching, as well as other non-manufacturing industries, such as banking institutions and service industries. Kaizen is originally a Japanese philosophy applied to all spheres of life, business and home, in order to continually improve them. Its core idea is to improve a process by carrying out small steps, continuously, day after day. This is in contrast with radical concepts like innovation or technical revolutions. The improvement is achieved by encouraging each employee to make small changes on a daily basis. The overall effect becomes a selection and improvement process for the entire organization. Kaizen also aims to improve production efficiency primarily through the humanization of the work place. The engineering of the work place proposed by this model is the 5S methodology: Seiri (sorting), Seiton (setting in order), Seiso (shining or regular cleaning), Seiketsu (standardization), Shitsuke (sustaining).
Measure, measure, measure!
These different processes were initially developed by the manufacturing industry but have since been applied to all sectors of the economy. A quality management system means also preparing, writing and updating a number of elements such as procedure catalogues, quality manuals, inspection and test procedures, work instructions, specifications, training plans and measurement records. All of these operating procedures interact together to produce goods and services with the quality required by customers. The elements of a quality management system should be stated clearly and documented in writing precisely. They should also be traceable back to the supplier or service providers.
Bureaucratization
The risk of immobilizing the processes and operation of any quality management system submerged under excessive rules and bureaucracy exists. Simplifying the process with accurate and adequate standard operating procedures (SOPs) can help avoid bureaucratization and quality issues. Perfect quality is achieved not when there is nothing more to add, but when there is nothing left to take away. A company or organization should strive for simplification to become agile. The speed and ability to learn and adapt are also key factors to improve quality; which is an important prerequisite for innovation and development in today’s complex world.
SOPs are documented practices that aim at ensuring consistency of processes and business operations. In the last article in this 3-part series we will talk about SOPs and learn some basic rules how to write them.
Sources
International Organization for Standardization ISO http://www.iso.org/iso/home/standards/management-standards/iso_9000.htm
Institut fédéral de métrologie (METAS) http://www.metas.ch/metasweb
European Committee for Standardization (CEN) https://www.cen.eu/about/Pages/default.aspx
EU Quality Assurance http://www.eqavet.eu/
American Society for Quality (ASQ) http://asq.org/index.aspx
International Association for Six Sigma Certification (IASSC) http://www.iassc.org/
European Foundation for Quality Management (EFQM) http://www.efqm.org/
Kaizen Institute http://www.kaizen.com/home.html
Wikipedia http://en.wikipedia.org/wiki/Quality_(business)
Lean Manufacturing Tools http://leanmanufacturingtools.org/34/lean-manufacturing-definition-2/
Lean Manufacturing Japan http://www.lean-manufacuring-japan.com/
Business Dictionary
United States Environmental Protection Agency http://www.epa.gov
Photo credit: Jaafar Alnasser Photography via photopin cc
Quel excellent article !
Lors d'un entretien avec ma coach professionnelle, nous avons abordé la possibilité pour moi de devenir une quality manager. Grâce à cet article, et en fonction de chacun des systèmes de gestion de la qualité décrits, j'ai pu me faire une idée globale du cahier des charges à assumer dans une telle fonction.
Je retiens qu'il y a une grande part de rédactionnel (principalement relatif aux procédures) à exécuter, ce qui m'effraie quelque peu. Mais je vais continuer à investiguer pour me faire une idée plus approfondie de ce métier.
Merci en tous les cas pour ces pistes !